

THE BENCHMARK IN FREEFORM MACHINING
Our flagship machine with up to 6-axes of ultra precision motion. It has been proven worldwide to be the most flexible, precise and user friendly ultra precision freeform diamond turning system available. With the main work spindle symmetrically integrated within an oil hydrostatic vertical Y-axis carriage, more advanced machining methods such as raster flycutting of linear diffractives and freeforms, micro-prismatic optical structures and micro-milling of aspheric lens arrays are achievable. This system has been engineered with the most complex surfaces in mind to enable you to compete in any optical ultra precision machining market.
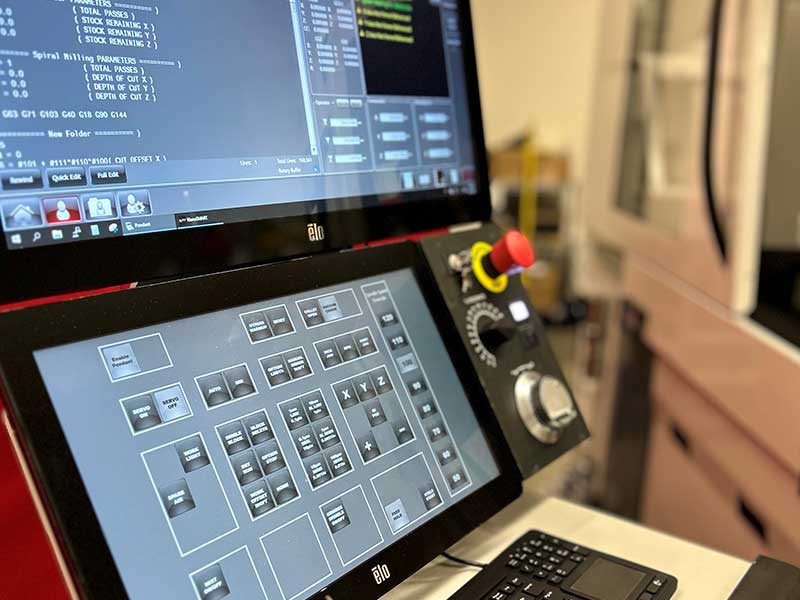
NanoSMART® Windows Based Interactive HMI Control System
This high speed 64 bit Delta Tau 1.2GHz Quadcore ARM based PowerPMAC controller is the industry’s leading touch / swipe gesture “smart” screen display. 5GB program file sizes, 4X increase in computational power compared to single core processor, rapid programming editing functions and 8 picometer feedback resolution. Three customizable 22” wide screens are accessible by swiping left or right keeping all the information you prefer at your finger tips. We welcome you to experience the difference with our most user friendly NanoSMART HMI.
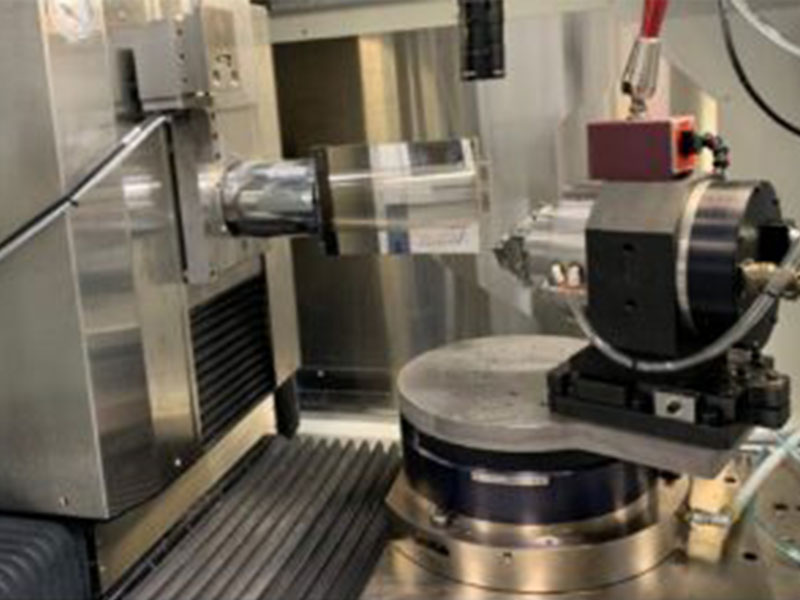
6 Axis Diamond Turning System
With the addition of our Oil Hydrostatic Rotary B-axis, A-axis, and optional C-axis of the work spindle, the 650FG is the only system capable of achieving up to 6-axes of ultra-precision motion. The versatility of this system in unmatched with advanced machining methods such as raster machining, flycutting, slow slide servo, micro-milling and micro-grinding.
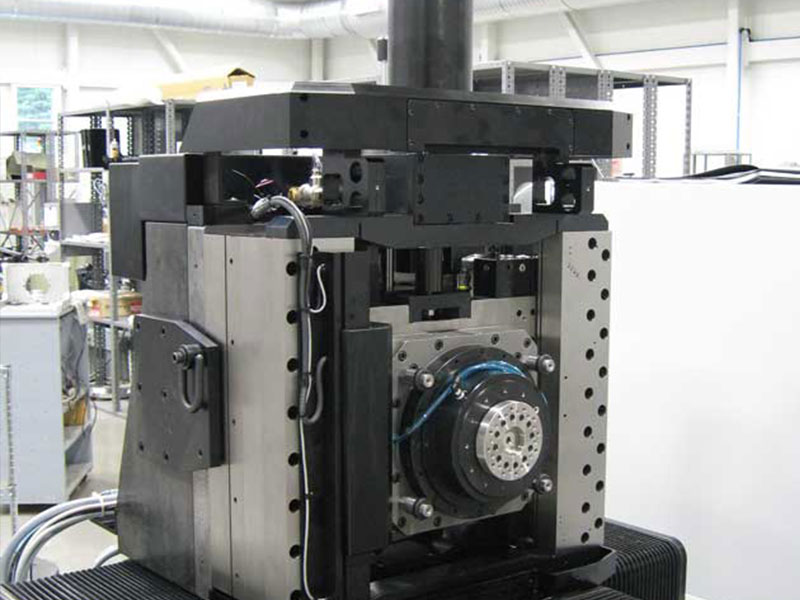
Symmetric Y-axis Design
Utilizes dual linear motors and an adaptively controlled, slot-compensated air bearing counterbalance assembly for optimal servo control of variable loads up to 85Kg (185 lbs @ 100psi) even with the Y-axis active. With the work spindle symmetry, the Y-axis carriage overall loop stiffness, reduced Abbe error, and proven thermal stability during lengthy raster machining cycles are unmatched in the industry. (see Features & Benefits Brochure)
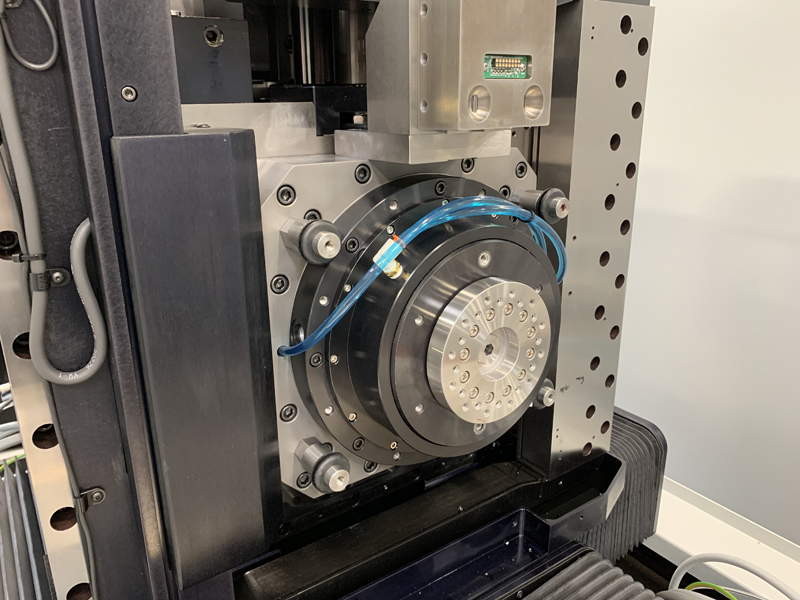
Exclusive “Impact Resistant” Air Bearing Work Spindle
This ideal center mounted thrust plate design, engineered for both heavy loads and high throughput applications, includes the exclusive added durability benefits of porous graphite. Motion accuracies are guaranteed to less than 12.5nm throughout its 10,000 rpm speed ran with total liquid cooling for long term thermal stability.
650FGv3 Freeform generator
MACHINE ACCESSORIES
ROTARY C-AXIS CAPABILITY FOR WORK SPINDLE
One of our most diverse and popular options which allows continuous path contouring using X, Z, & C axes. This option is used for single point diamond machining of toric & freeform surfaces via Nanotech’s “Slow-Slide-Servo” (S³) machining process. Note: S³ machining requires Nanotech’s NanoCAM4-3T or suitable software for generation of X, Z, C file formats.
OIL HYDROSTATIC ROTARY B-AXIS
Fully constrained oil hydrostatic rotary bearing option. This axis utilizes a direct drive brushless DC rotary motor and high resolution encoder. Positioning accuracy of +/- 1.0 arc second and feedback resolution of 0.005 arc seconds. Radial and axial motion errors are guaranteed to ≤ 100nm. Includes pneumatic / mechanical brake.
ROTARY A-AXIS
The rotary air bearing A-Axis sits on top of the oil hydrostatic B-axis. It utilizes a direct drive brushless DC rotary motor and high-resolution encoder. Positioning accuracy of +/- 1.0 arc second and feedback resolution of 0.01 arc seconds. Compatible with NanoCAM4.
POLAR TOOL COORDINATE (PTC)
B-axes are typically used for Tool Normal Machining, whereby the diamond tool tip is positioned over the center of B-axis following Nanotech’s simple procedure. PTC is an optional programming software package that facilitates tool setups by allowing the center of the tool radius to be offset from the center of rotation of the B axis.
OPTICAL TOOL SETTING SYSTEM
Complete cable free system with integrated power & I/O communications. Features Nanotech’s Automatic Edge Detection Technology which eliminates the need for manual selection of data points on cutting edge. The result is faster and more accurate tool setting. Light weight at 2Kg (4 lbs) and able to find tool center position and radius quickly to less than 1µm total system repeatability.
NanoCAM4 PROGRAMMING SOFTWARE
The most comprehensive ultra precision CAM Programming software available. A result of decades of customer interactions and diamond turning industry expertise, N4 compliments the many advanced capabilities of Nanotech’s systems of today and in the future.
WORKPIECE MEASUREMENT AND ERROR COMPENSATION SYSTEM (WECS)
With free software upgrades for life via our FTP site, WECS is a valuable accessory upgrade for on machine form measurement & correction to less than 0.1µm. WECS has continuously evolved to improve both efficiency and capabilities. Recent additions include the ability to bypass a hole at center, a skip point function for fast surface measurements, and freeform data capturing.
NFTS-6000 FAST TOOL SERVO
Our Fast Tool Servo (NFTS-6000) is used for machining of specific freeform applications such as micro-structuring on surfaces. This closed loop system has 6mm of total travel (+/-3mm). It includes a custom micro-height adjustment stage with +/- 2.58 mm travel and adjustment resolution of 0.14 µm/degree (5.6µ”/degree). NanoCAM4³T freeform programming software is required.
TEMPERATURE CONTROLLED AIR SHOWER
Our latest Air Shower Temperature Control System is capable of providing a 20:1 improvement in temperature variation for the machine’s upper enclosure. Features Solid State Thermo Electric Technology (TEC) thereby eliminating the need for any refrigerant coolant!
10K RPM GRINDING SPINDLE
The 10,000 RPM grinding spindle is an air bearing motorized design that can handle larger size grinding wheels for larger components or larger size fly-cutting wheels for raster machining. The spindle is liquid cooled for thermal stability.
60K RPM MILLING/GRINDING SPINDLE
This 60,000 RPM spindle is an air bearing motorized design that can handle small to medium size grinding wheels. It is also the preferred choice for optical micro-milling applications such as aspheric lens arrays. The spindle is liquid cooled for thermal stability.
CNC CONTROLLED DRESSING/PROBE STATION
Provides on-machine grinding wheel dressing and LVDT probe measurement all under CNC control utilizing the 650FG’s own vertical oil hydrostatic Y-axis.
FLOOD COOLANT PUMPING SYSTEM
This coolant pumping system is used in applications where flood coolant is desired. The system is capable of delivering precision controlled coolant flow to the desired cutting zone. Unit can also supply temperature controlled coolant through the addition of an optional chiller system.
VACUUM CHUCKS
Three different size vacuum chucks are available. These aluminum chucks are typically mounted to the workspindle and contain 12 radial balancing holes. (100, 150, or 200mm diameter available).
FLYCUTTER HEADS
We offer two fly-cutting heads designs. The simplest form is shown here and is typically used for raster machining. The second design allows for independent adjustment of rake and tow on the diamond tool.
WORK SPINDLE CHILLER
Spindle chillers are required for thermal stability of the main work spindle and also any grinding or milling spindles. This chiller operates at 200 / 230 V single phase plugs into a dedicated outlet. It is integrated on the machine controller for performance monitoring.
NanoBALANCE® SOFTWARE
Displayed on machine controller for assisting the user in dynamic balancing of the work spindle. NanoBalance offers a flexible user interface that supports the most common balancing methods including single weight, test mass & balance screws.
NanoMETER®
Three channel On-Screen digital amplifier is available for use with LVDT probes and the electronic gage head. This software comes standard with WECS package or can be purchased as a separate accessory.
ELECTRONIC GAUGE HEAD/MAGNETIC STAND
Commonly used to indicate part diameters or precision fixtures to position their centers on (optical) axis of the work spindle. Works with NanoMETER on screen amplifier gauge.
SOLID TOOL HOLDER
The 650 FG has available a solid tool holder for the diamond tool. When using this tool post, the height adjustment is made by utilizing the machine’s Y-axis. Alternatively, Nanotech’s flexure design Micro-Height Adjust Tool Holder (see photo inset) can also be used.
DUAL NOSE TOOL HOLDER
Ideal for small part production applications so multiple diamond tools can be set-up to optimize the available space on Z-axis table. Independent coarse & fine tool height adjustment. Includes base plate spacer for proper nominal tool height.
OPTICAL OBSERVATION PACKAGE
Used to safely monitor machining inside the enclosure environment. Image is displayed using the Observation Module on a NanoSMART HMI. Images and / or videos are easily captured. Manual focus / zoom camera with 1.3MP Resolution.
SPRAY MIST COOLANT SYSTEM
Complete system with tank, spray nozzles and magnetic mixer base to deliver smooth flowing coolant to the cutting surface. The standard system includes two nozzles, but can be configured with 2, 4 or 6 independently programmable mist nozzles.
STAINLESS STEEL COOLANT SHROUD
Mounts directly to the spindle housing to minimize cleanup time. Captures majority of slurry & chips throughout the machining process. Ideal for IR lens production, the shroud features a removable top half for easy access to the workpiece.
SELF LEVELING SYSTEM
Provides self maintenance of the machine’s air isolation system to ensure both proper float and table levelness as weight is added or removed from either the Z-axis slide or main work spindle.
PART CENTERING DEVICE (PCD)
Eliminate manually indicating of each part. Accurately position your parts on the spindle centerline automatically. Positioning accuracy to 1µm is accomplished within 30 seconds when starting from a decentered value of 0.5mm. User friendly software with 3 operation modes.
HIGH RESOLUTION 3D TOUCH PROBE
Enables on-machine mechanical measurement of diameters and center thicknesses via a ruby tipped probe with a resolution of +/- 0.25μm. Measurements can be linked directly to production part programs for automatic adjustment when needed prior to removing the finished part from the spindle.
HAND HELD OPERATOR PENDANT
This hand held controller provides the operator with the flexibility of having a portable remote pendant. Its long cord provides ample freedom to adjust axes positions while being close to the workpiece. Includes docking station for storage when not in use.
NanoTEMP
Portable 16 channel precision temperature monitoring system. Software is included as part of our Air Temperature Control System or this accessory can be purchase as a separate stand alone item. Multiple probe options available.
SHEAR DAMPED
AIR ISOLATION SYSTEM
An optional upgrade to our standard air isolation system. Shear Damped Air Isolation provides a reduced natural frequency for either facility installations where lower frequency floor vibrations are present or high electro optics applications where such a system may be beneficial.
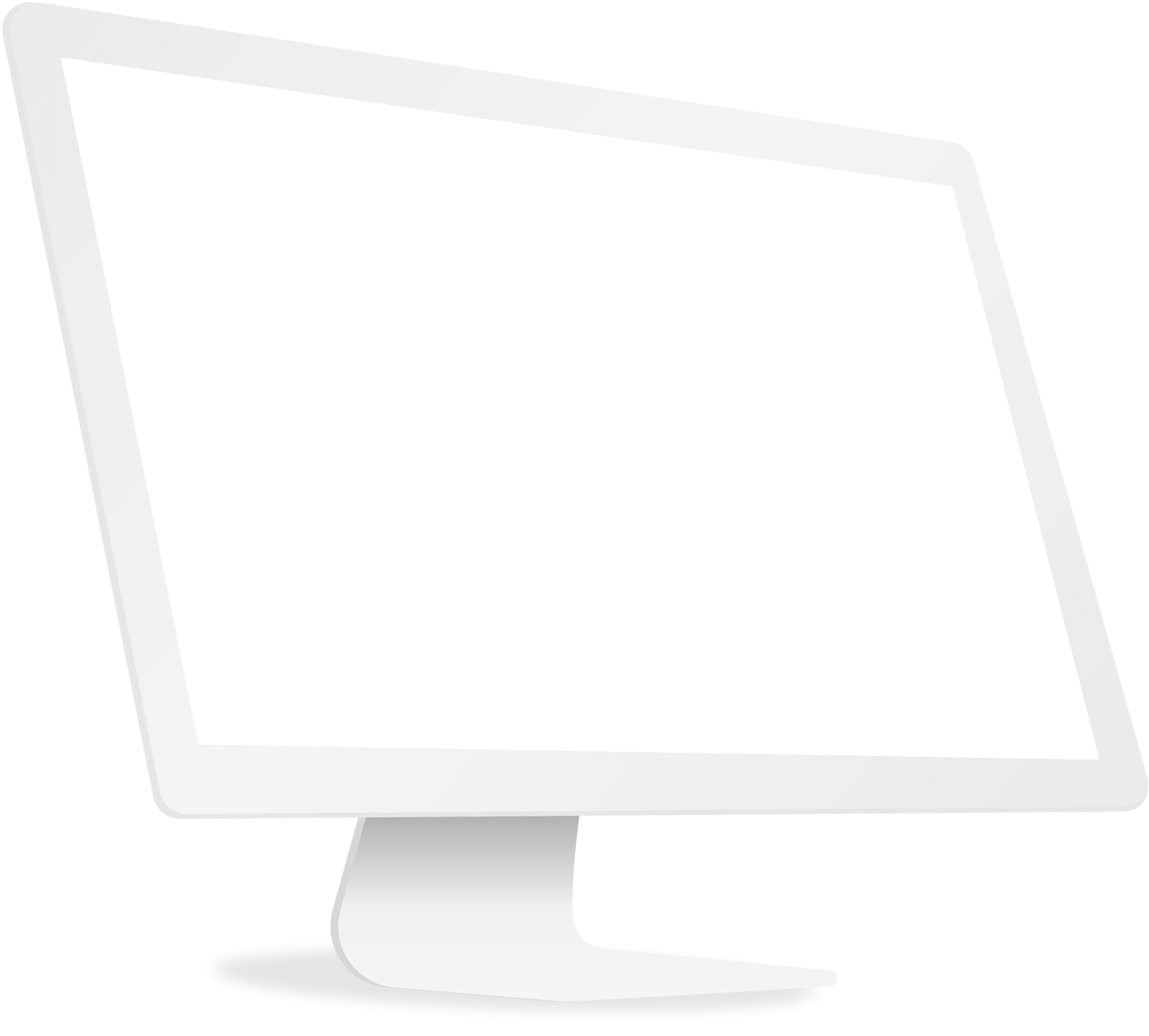
WE QUANTIFY RESULTS THE WAY YOU DO!
Always measured on the same surface, after same finish pass.
Sub-nanometer Surfaces Finishes, Sub-micron Form
Directly Off the Machine in a Wide Variety of Materials!
Diamond Turned XZ Standard Acceptance Test Part