
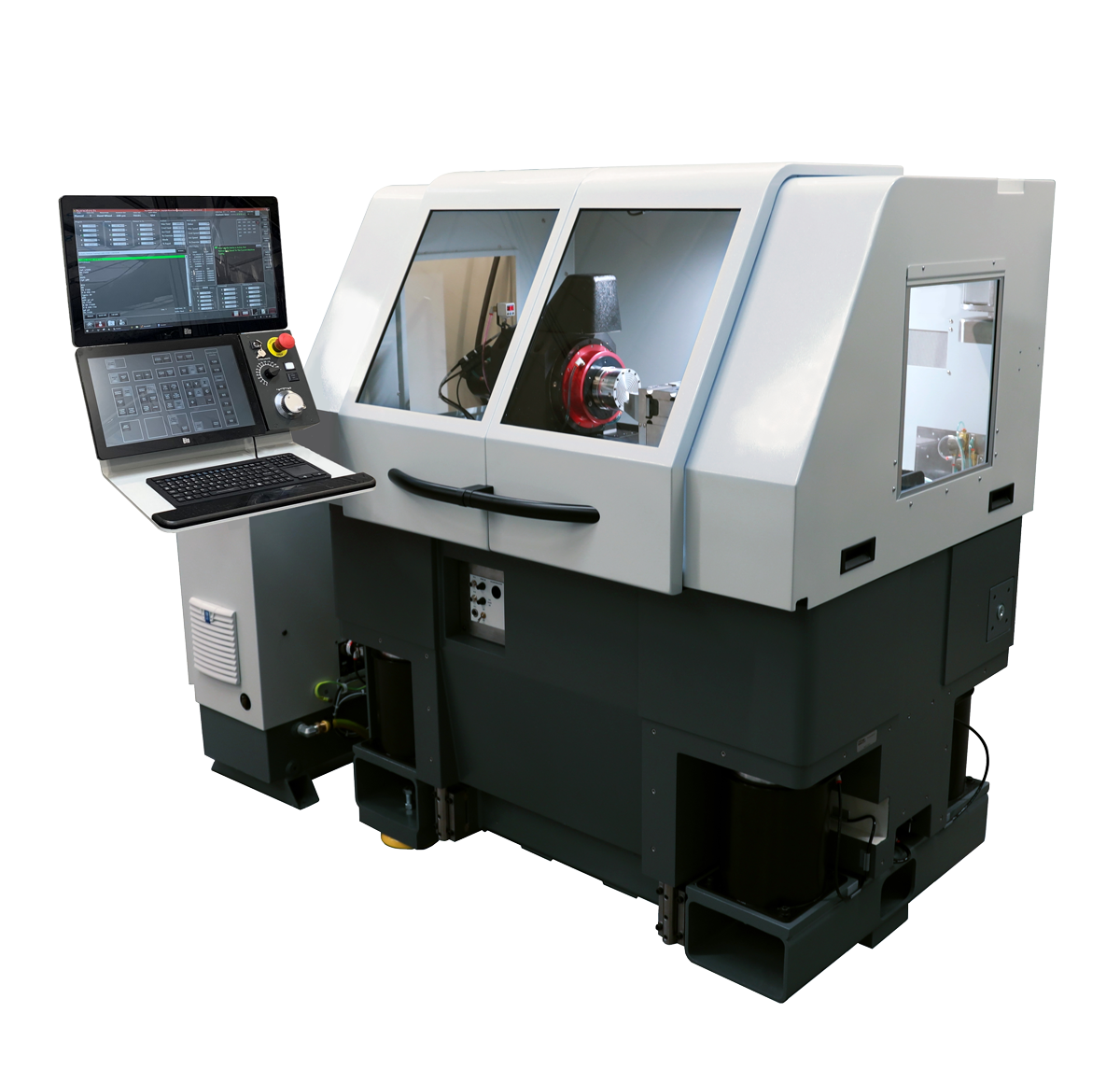
The Ultimate Performance in Mold Pin Machining
Used for the rapid production of spherical & aspheric optical lenses, mirrors, mold pins, freeform optics and even mechanical components. If your application fits within a 350mm diameter window (with optional riser package), this machine may be the ideal solution for your ultra precision needs.
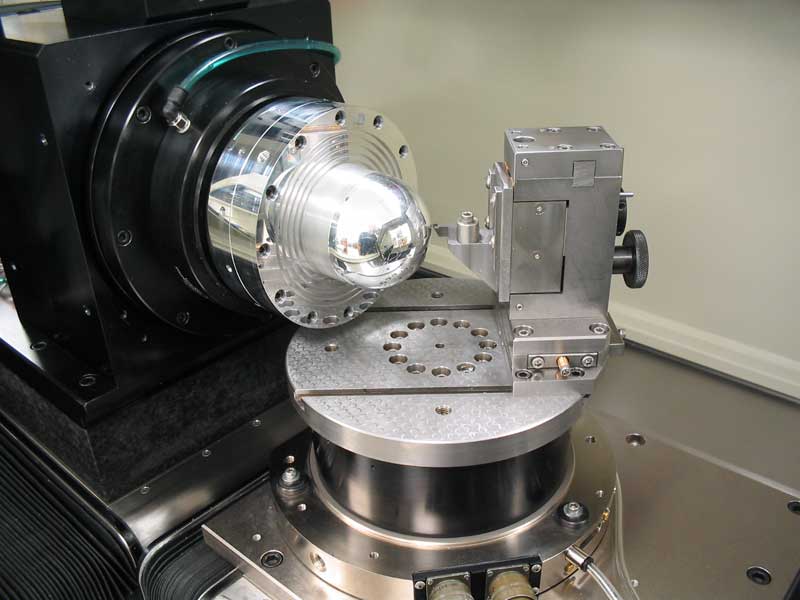
Optional C Rotary with
Linear Y or Rotary B Axis
Expansion of the basic 2-axis system is simple. One can have up to 4 axes of continuous path motion via the addition of C & B or C & Y. The C-axis motion control of the work spindle enables toric, biconic, and other freeform surfaces to be machined “on-axis” via our Slow Slide Servo (S3) process. Our Air Bearing Rotary B or removable Oil Hydrostatic Vertical Linear Y-axis can be configured independently on the Z-axis carriage for future added flexibility.
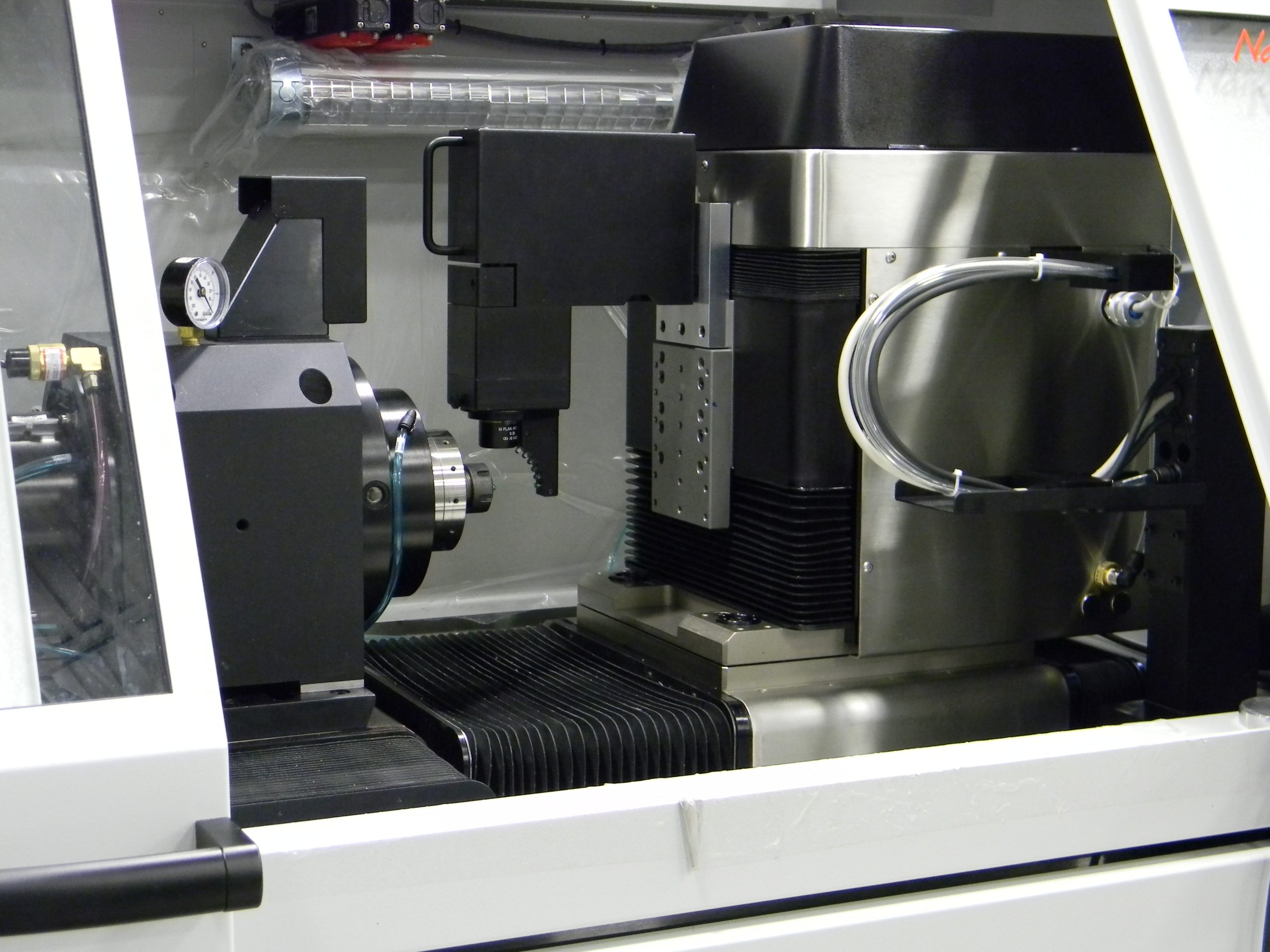
Mechanical Design Strengths
The upper enclosure is engineered to overlap the inner protective stainless steel apron of the system keeping all swarf / coolant within the desired machining area. Large dual sliding doors allow easy access to the entire work area. Both sliding doors overlap when closed and then simply slide to a “full open” position for easy cleaning / maintenance of the machine’s entire interior. This system has a natural granite base structure with passive air isolation system. High stiffness and low profile “box-way” style oil hydrostatic slide ways with linear motor drives are engineered into a low center of gravity framework for maximum mechanical stability.
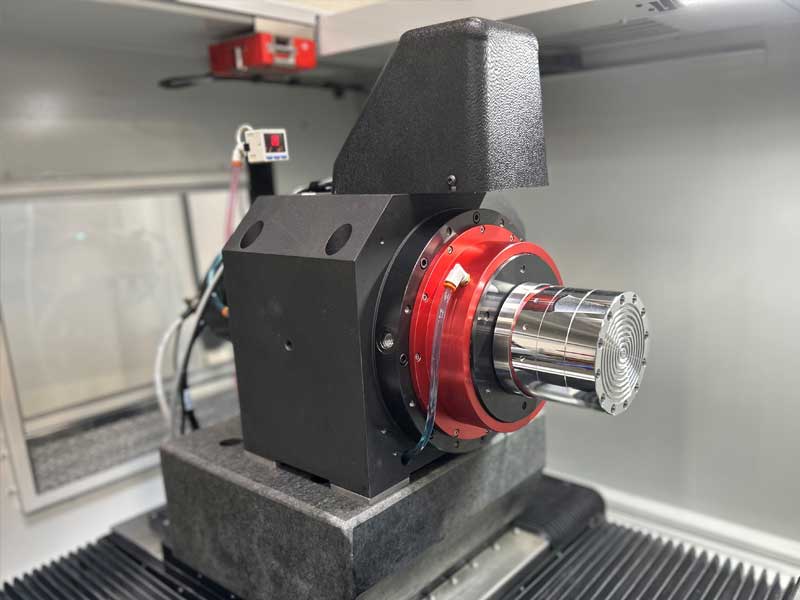
Exclusive “Impact Resistant”
Air Bearing Work Spindle
This ideal center mounted thrust plate design, engineered for both heavy loads and high throughput applications, now includes the added benefits of porous graphite. Motion accuracies are guaranteed to less than 12.5nm throughout its 10,000 rpm speed range with total liquid cooling for long term thermal stability.
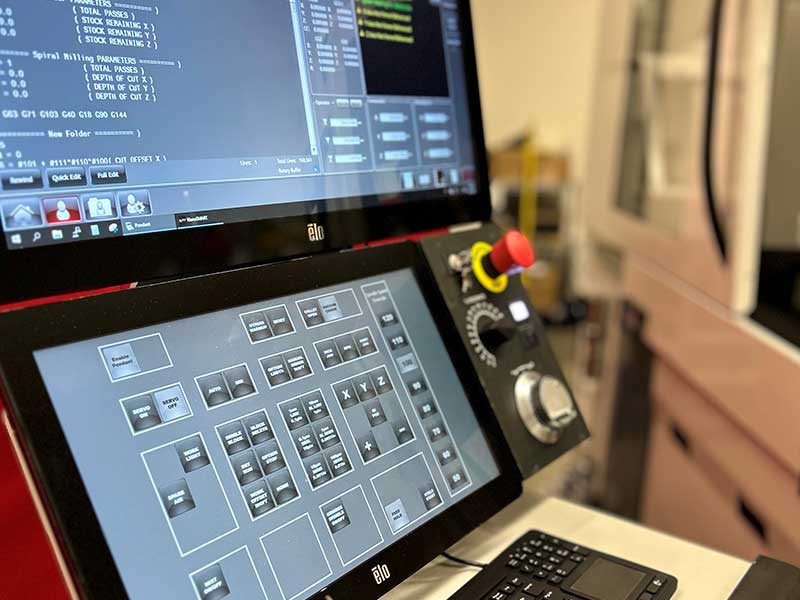
NanoSMART® Windows Based Interactive HMI Control System
This high speed 64 bit Delta Tau 1.2GHz Quadcore ARM based PowerPMAC controller is the industry’s leading touch / swipe gesture “smart” screen display. 5GB program file sizes, 4X increase in computational power compared to single core processor, rapid programming editing functions and 8 picometer feedback resolution. Three customizable 22” wide screens are accessible by swiping left or right keeping all the information you prefer at your finger tips. We welcome you to experience the difference with our most user friendly NanoSMART HMI.
250UPLMPv3 LATHE STYLE
MACHINE ACCESSORIES
ROTARY C-AXIS CAPABILITY FOR WORK SPINDLE
One of our most diverse and popular options which allows continuous path contouring using X, Z, & C axes. This option is used for single point diamond machining of toric & freeform surfaces via Nanotech’s “Slow-Slide-Servo” (S³) machining process. Note: S³ machining requires Nanotech’s NanoCAM4-3T or suitable software for generation of X, Z, C file formats.
OIL HYDROSTATIC ROTARY B-AXIS
Fully constrained oil hydrostatic rotary bearing option. This axis utilizes a direct drive brushless DC rotary motor and high resolution encoder. Positioning accuracy of +/- 1.0 arc second and feedback resolution of 0.005 arc seconds. Radial and axial motion errors are guaranteed to ≤ 100nm. Includes pneumatic / mechanical brake.
REMOVABLE OIL HYDROSTATIC VERTICAL LINEAR Y-AXIS
Removable Y-axis for the Nanotech 250 or 450UPL. This oil hydrostatic vertical slide has 100mm of vertical travel, 0.01 nanometer programming and 8 picometer feedback resolution. It also features an adaptive air bearing counterbalance for optimum performance when adding and removing parts from its mounting shelf.
POLAR TOOL COMPENSATION
Tool Normal machining typically requires the cutting tool to be positioned precisely over the center of the B Axis. Using PTC, in combination with our Optical Tool Setting System, the tool can simply be mounted anywhere on top of B-axis, eliminating the time required for a precision tool setup at the center of B. Our PTC technology then uses coordinated X, Z and B-axis motions to simulate an alternate axis of rotation about the tool radius’ center position. G codes are used to activate and de-activate PTC within part programs.
NanoCAM4 PROGRAMMING SOFTWARE
The most comprehensive ultra precision CAM Programming software available. A result of decades of customer interactions and diamond turning industry expertise, N4 compliments the many advanced capabilities of Nanotech’s systems of today and in the future.
WORKPIECE MEASUREMENT AND ERROR COMPENSATION SYSTEM (WECS)
With free software upgrades for life via our FTP site, WECS is a valuable accessory upgrade for on machine form measurement & correction to less than 0.1µm. WECS has continuously evolved to improve both efficiency and capabilities. Recent additions include the ability to bypass a hole at center, a skip point function for fast surface measurements, and freeform data capturing.
NFTS-6000 FAST TOOL SERVO
Our Fast Tool Servo (NFTS-6000) is used for machining of specific freeform applications such as micro-structuring on surfaces. This closed loop system has 6mm of total travel (+/-3mm). It includes a custom micro-height adjustment stage with +/- 2.58 mm travel and adjustment resolution of 0.14 µm/degree (5.6µ”/degree). NanoCAM4³T freeform programming software is required.
OPTICAL TOOL SETTING SYSTEM (OTS)
Our latest Air Shower Temperature Control System is capable of providing a 20:1 improvement in temperature variation for the machine’s upper enclosure. Features Solid State Thermo Electric Technology (TEC) thereby eliminating the need for any refrigerant coolant!
TEMPERATURE CONTROLLED AIR SHOWER
Our latest Air Shower Temperature Control System is capable of providing a 20:1 improvement in temperature variation for the machine’s upper enclosure. Features Solid State Thermo Electric Technology (TEC) thereby eliminating the need for any refrigerant coolant!
ROTARY C-AXIS CAPABILITY FOR WORK SPINDLE
One of our most diverse and popular options which allows continuous path contouring using X, Z, & C axes. This option is used for single point diamond machining of toric & freeform surfaces via Nanotech’s “Slow-Slide-Servo” (S³) machining process. Note: S³ machining requires Nanotech’s NanoCAM4-3T or suitable software for generation of X, Z, C file formats.
OIL HYDROSTATIC ROTARY B-AXIS
Fully constrained oil hydrostatic rotary bearing option. This axis utilizes a direct drive brushless DC rotary motor and high resolution encoder. Positioning accuracy of +/- 1.0 arc second and feedback resolution of 0.005 arc seconds. Radial and axial motion errors are guaranteed to ≤ 100nm. Includes pneumatic / mechanical brake.
REMOVABLE OIL HYDROSTATIC VERTICAL LINEAR Y-AXIS
Removable Y-axis for the Nanotech 250 or 450UPL. This oil hydrostatic vertical slide has 100mm of vertical travel, 0.01 nanometer programming and 8 picometer feedback resolution. It also features an adaptive air bearing counterbalance for optimum performance when adding and removing parts from its mounting shelf.
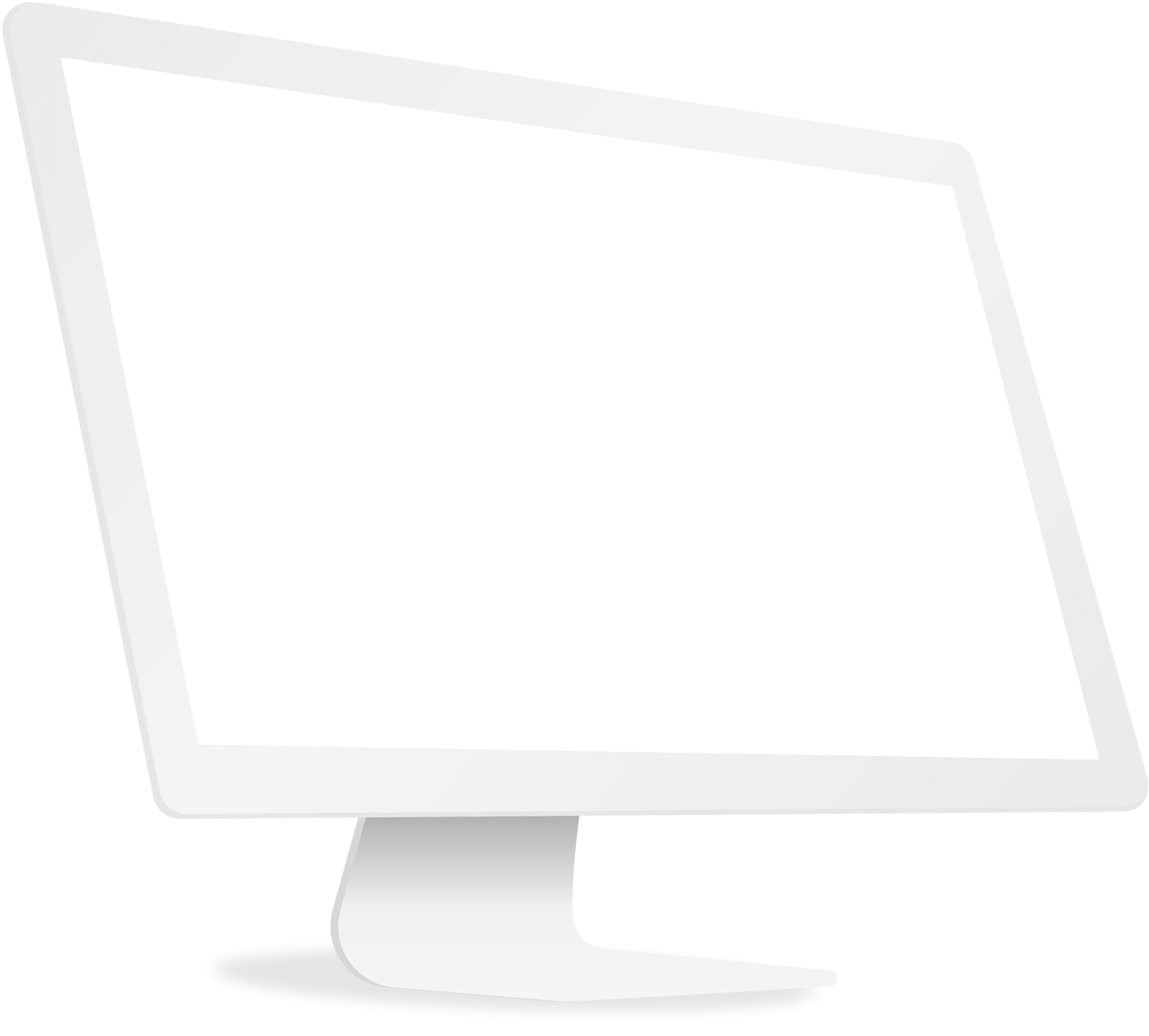
WE QUANTIFY RESULTS THE WAY YOU DO!
Always measured on the same surface, after same finish pass.
Sub-nanometer Surfaces Finishes, Sub-micron Form
Directly Off the Machine in a Wide Variety of Materials!
Diamond Turned XZ Standard Acceptance Test Part